|
 |
 |
 |
 |
 |
 |
 |
 |
 |
 |
 |
 |
 |
 |
 |
 |
|
 |
|
|
|
Zwei neue Ammoniak-Kältemaschinen im Schweizerischen Bankverein (neu UBS AG) Basel
Das Verwaltungsgebäude der UBS in der Gartenstrasse 9 in Basel verfügt über zwei Turbokaltwassersätze mit je ca. 1300 kW. Zur Ergänzung waren zwei Kolbenkältemaschinen mit je 260 kW Leistung installiert, welche die
Wintergrundlast abdecken sowie zu geringe Teillasten der Turbos vermeiden sollen. Nachdem bereits vor einigen Jahren bei der Umstellung von Elektrospeicherheizung auf Fernwärme einer der beiden 68m³-Heizungsspeicher
zum Kältespeicher "umisoliert" und mit dem Kältenetz verbunden worden war, wurde er nun im Rahmen einer umfangreichen Revision der Kälteerzeugung aktiviert. Da bei den kleinen Kältemaschinen in zunehmendem
Masse Verdichterschäden auftraten, entschloss sich die Bauherrschaft, die Maschinen auszuwechseln, zumal diese noch mit R500 - einer Mischung aus R12 und R152a - betrieben wurden.
Warum Ammoniak als Kältemittel?
Die Wahl fiel auf dieses Kältemittel zum einen aufgrund seiner Eigenschaften hinsichtlich Ozonzerstörungs- und Treibhauspotential, zum anderen wegen der hinreichend bekannten physikalischen bzw. thermodynamischen
Vorzüge. Trotz seiner Gefährlichkeit erscheint dieses Kältemittel als die beste Wahl, zumal es eine hohe Warnwirkung hat (Geruchsschwelle bei 10% des MAK-Wertes) und durch Überwachungs- und Sicherheitseinrichtungen
entsprechende Vorsorge getroffen werden kann. Es ist ausserordentlich wichtig, dass man mit dem Kältemittel Ammoniak richtig umgeht, wobei die Erfahrung der Erstellerfirma eine wesentliche Rolle spielt.
Besonderes Augenmerk wurden auch den Arbeitsprinzipien geschenkt. Setzen die einen Hersteller auf Trockenverdampfung, um die Kältemittelmenge gering zu halten, wird bei den anderen der überflutete Betrieb bevorzugt. Hierbei kann auf die Überhitzung verzichtet werden (mechanische Tropfenabscheidung), was v.a.im Teillastbetrieb vorteilhaft ist, da die Temperaturdifferenz im Wärmetauscher beliebig klein gehalten werden kann. Ausserdem ist die Regelung stabiler und weniger störungsanfällig (kein Expansionsventil). Der Nachteil ist die grössere Kältemittelfüllmenge (50-100% mehr, je nachdem, welche Lieferanten verglichen werden) sowie der etwas höhere Preis. Letzterer wird jedoch durch geringere Betriebskosten (günstigere Fahrweise aufgrund geringerer Temperaturdifferenzen) wieder aufgewogen.
Um bei überflutetem Betrieb die Kältemittelmenge klein zu halten, müssen Plattenwärmetauscher verwendet werden. Über die Dichtungen nicht verschweisster Plattenwärmetauscher sowie der Flansche diffundieren wegen den
ungleichen Partialdrücken immer kleine Mengen Ammoniak aus, weshalb hier vollverschweisste PWT zum Zuge kamen.
Unerprobte technische Lösungen haben in der letzten Zeit gelegentlich zu Ammoniakaustritten aus Kältesystemen geführt. Besonders die Systeme mit Trockenexpansion und löslichen Kältemaschinenoelen haben für viele
O-Ring-Dichtungen und Wellenabdichtungen an den Verdichtern neue Probleme hervorgerufen, welche zu deren Ausfall führten.
Weitere Gefahren entstehen durch Ansaugen von flüssigem Kältemittel in den Verdichter; dies passiert bei überfluteten Systemen nur dann, wenn zu viel Kältemittel eingefüllt wird. Bei Systemen mit Trockenverdampfung,
das heisst mit Expansionsventilen, ist die Gefahr von Flüssigkeitsschlägen im Verdichter bei Versagen dieses Ventils weitaus grösser.
Das gewählte Konzept
Nach ausführlichen Diskussionen wurde folgendes Anlagenkonzept gewählt:
- überfluteter Betrieb mit zylindrischen Plattenwärmetauschern für Verdampfer und Kondensator, Platten V4A vollverschweisst
- Schraubenverdichter
- Abwärmenutzung von den Ölkühlern
- Einsatz eines nicht kältemittellöslichen Öles, automatische Ölrückführung
Technische Daten pro Maschine
- Kälteleistung 6/12°C:258 kW
- Ölkühler :30 kW
- Kondensator 27/37°C:285 kW
- Leistungsbedarf Verdichter:57 kW
- COP:4,53
|
|
|
 |
|
|
|
Eine WRG-Nutzung der Kondensationswärme im vorhandenen 48/38°-Netz war nur schlecht möglich. Die Kondensationsdrücke wären sehr hoch geworden , was sich massiv auf die Lebensdauer der Maschinen ausgewirkt
hätte. Stattdessen wird nun die Abwärme der Ölkühler genutzt, denen ein Notkühler vorgeschaltet ist, um bei mangelndem Wärmebedarf die Ölwärme via Rückkühlnetz über Dach abzuführen. Im Gegensatz zu einem WRG-Betrieb
ist die Nutzung der Abwärme aus dem Öl nicht mit einem vermehrten Primärenergieeinsatz verbunden, da der COP unbeeinflusst bleibt.
Die Leistung kann stufenlos von 25 bis 100% variiert werden (Leistungsschieber), wobei das übergeordnete Energiemanagement via Speicherbewirtschaftung dafür sorgt, daß die Maschinen möglichst auf Vollast
gehalten werden.
|
|
|
|
Die Steuerung
Die Maschinensteuerung musste als SPS mit dem gleichen Fabrikat wie die Gebäudeleittechnik ausgeführt werden (GE Fanuc). Auch wurde für die Programmierung der Steuerung vorgeschrieben, dass sie durch Fa.R.Knecht
& Co. in Brüttisellen erstellt wird, welche auch die übergeordnete Leittechnik programmiert. Es ist nicht üblich, daß die Maschinenhersteller auf eine solche Konstellation eingehen. Aufgrund der vorbehaltlosen
Mitarbeit der Fa.Wettstein hat sich diese Vorgehensweise nach Einschätzung aller Beteiligten jedoch hervorragend bewährt. Es gab keine Schnittstellen- und Kommunikationsprobleme zwischen Maschinensteuerung und
Leitebene. Die Maschinen-Tableaux verfügen über einen gemeinsamen Touch-Screen, auf dem menügeführt zum einen sämtliche Ist- und Sollwerte zusammen mit einem Anlagenschema übersichtlich dargestellt sind, zum anderen
auch noch als Tabelle abgerufen werden können. Passwortgeschützt können die Sollwerte auch verändert werden.
|
|
|
|
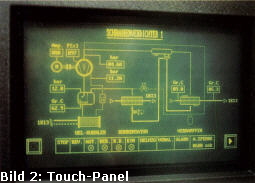 |
|
|
|
Die Sicherheitsvorkehrungen
Aus Platzgründen schied eine Vollkapselung der Maschinen von vorherein aus. Statt dessen wurde der Standort der Maschinen durch eine gemauerte Wand von der restlichen Zentrale abgetrennt. Sämtliche
Rohrdurchführungen wurden gasdicht ausgeführt, ebenso Zu- und Fortluftklappe. Der Raum wird durch Ammoniakwächter überwacht. Zur Ausscheidung von Ammoniak aus der Luft wurde ein Ammoniakwäscher installiert. Hierbei
handelt es sich um eine Füllkörperkolonne. Bei Überschreiten von 500 ppm werden die Lüftungsklappen geschlossen, der Ammoniakwäscher geht in Betrieb, saugt die Luft aus dem Raum und leitet sie im Gegenstrom mit dem
Waschwasser durch die Füllkörper. Steigt die NH3-Konzentration weiter, werden bei Überschreiten von 1000 ppm die Kältemaschinen abgestellt. In beiden Fällen erfolgt Alarmierung auf die PSA. Über einen
Umstellhahnen kann das kontaminierte Waschwasser nach einem Havariefall mit der Wäscherpumpe zur Entsorgung in einen Stapelcontainer umgepumpt werden.
Die Sicherheitseinrichtungen wurden an einem Wochenende einem Test unterzogen. Der Maschinenraum wurde mit 1 kg gasförmigem NH3 befüllt, was einer Konzentration von ca. 12’000 ppm entspricht. Das Gas wurde mit einem Transportventilator im Raum verteilt. Anschliessend wurde der Luftwäscher gestartet und in periodischen Abständen über eine Kontrollöffnung in der Türe die NH3-Konzentration
mittels Dräger-Prüfröhrchen gemessen. Am Ende des Auswäschvorganges, d.h. nach 37 min. und Erreichen einer Konzentration von ca. 400 ppm, konnte der Raum bei starkem NH3-Geschmack betreten werden. Nach
kurzem Lüften des Maschinenraumes war kein NH3-Geschmack mehr wahrnehmbar. Im Gebäudeinneren waren ausserhalb des Maschinenraumes zu keinem Zeitpunkt des Versuches NH3-Emissionen wahrnehmbar.
|
|
|
|
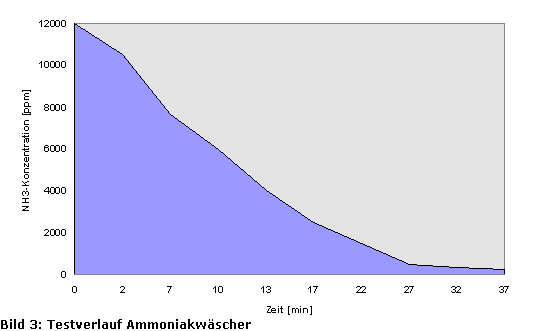 |
|
|
|
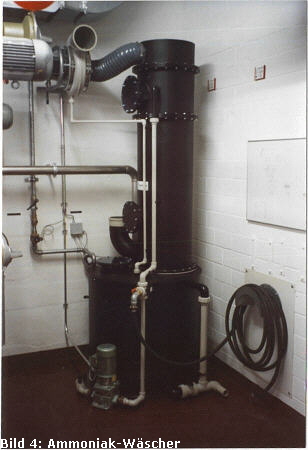 |
|
|
|
Isolation
Aufgrund der intensiven Diskussionen hinsichtlich Unbedenklichkeit der Mineralwolle wurde als Isolation für die WRG-Leitungen Schafwolle genommen. Diese wird noch nicht in Form von Halbschalen angeboten, sondern als
Matten in unterschiedlichen Dicken, die dann entsprechend zugeschnitten werden müssen. Dies bedeutet einigen Mehraufwand, der jedoch, da er im Hinblick auf das Gesamtbudget des Projektes im Promillebereich liegt,
ebenso wie die höheren Materialkosten vertretbar erschien. Da das vielfach als Brandschutzmittel verwendete Borsalz bei auftretender Feuchtigkeit die Rohrleitungen angreift, wurde auf ein Fabrikat zurückgegriffen,
das aufgrund der Verfilzungsmethode auch ohne Borsalz die notwendige Brandsicherheit bietet.
Betriebserfahrungen
Die Maschinen laufen quasi im Dauerbetrieb. Sie liefen vom ersten Moment an praktisch störungsfrei; einzige Störung war ein Defekt am Weggeber des Leistungsschiebers. Ausserdem traten Undichtigkeiten bei den
Wellenabdichtungen auf. Sie waren jedoch bedingt durch eine Veränderung der Ölzusammensetzung, die vom Öllieferanten nicht mitgeteilt wurde, sodaß die O-Ringe nach kurzer Zeit aushärteten. Durch einen entsprechenden
Wechsel des O-Ring-Materials konnten diese Schwierigkeiten aus dem Weg geräumt werden.
|
|
|
|
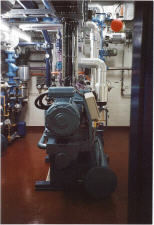 |
|
|
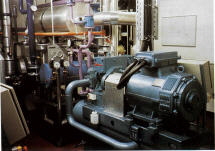 |
|
|
|
|
 |
|
|
|
|
 |
 |
|
Webdesign: J.Pritzel
|
|
|